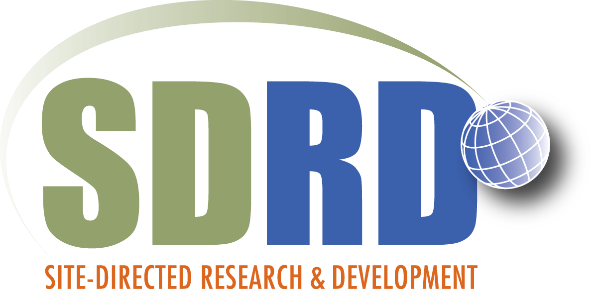
Additive Manufacturing of Structural and Pixelated/ Discriminating Scintillators
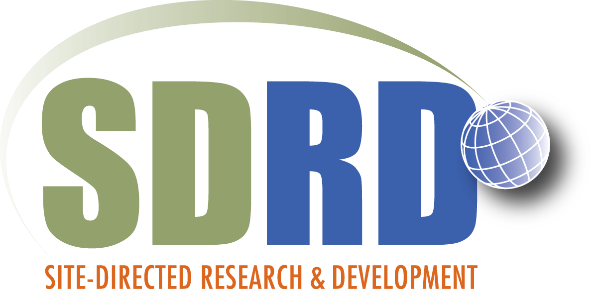
Project # 23-019 | Year 1 of 2
Matthew Staskaa, Adam Wolvertonb, Jim Tinsleya, Rob Bucklesb, John DiBenedettoa
aSpecial Technologies Lab (STL), bNevada National Security Sites (NNSS)
This work was done by Mission Support and Test Services, LLC, under Contract No. DE-NA0003624 with the U.S. Department of Energy, the NNSA Office of Defense Programs, and supported by the Site-Directed Research and Development Program. DOE/NV/03624–1905.
Abstract
Plastic scintillators are commonly used in radiation detection devices within the Nevada National Security Sites (NNSS) and by its customers. Additive manufacturing (AM) of plastic scintillators has been recently shown to produce performance comparable to cast materials. This work has been extended into composites using nanoparticles and sintered composites. The fine detail found in current state-of-the-art AM systems allows for truly mixed materials and engineered structures not available by other means. We are extending these rather nascent advances into the engineering of shapes that function as structural components, gradients in material index (by composition) to improve optical coupling and combinations of spatial and spectral aspects to increase discrimination.
Background
The work within this Site-Directed Research and Development (SDRD) project aims to develop a capability at the NNSS that can AM plastic scintillators for prototyping and quick turnaround mission requirements. This capability could allow the NNSS to develop customizable scintillators. These engineered scintillators could have integral light guides, inherently removing the lossy interfaces, and optimizing the index matching to photodetectors, etc. through gradients in scintillator composition. Also, there could be a wider use of AM to fabricate more complex shapes that can create structural components in covert or size, weight, and power (SWaP)-limited applications.
Technical Approach
Currently, plastic scintillators consist of a solid solution of organic scintillating molecules dissolved in a polymerized solvent. This mixture is typically cast into large ingots of material, which can take a long time to cure, and special care may be needed to ensure the material is void of air bubbles. Once the material is fully cured, it then must be fabricated or machined to the desired geometry, polished to a desired finish, and may require a final thin film coating depending on the desired light reflection/timing characteristics of the scintillator system. Technical limitations often stem from the need to meet tolerancing of complex geometries depending on the application.
AM plastic scintillators have been recently shown to produce performance comparable to cast materials. Recent advances in AM techniques allow a user to design components that can be functionally graded, where specific properties can vary within the component itself, referred to as functionally-graded materials (FGM). Our work plans to use these advances to produce seamless yet segmented scintillator shapes for better optical performance and/or that serve as structural components. This work will leverage recent advances in AM scintillators at Lawrence Livermore National Laboratory, the US Naval Academy (USNA), and our own work on nanoparticle scintillators. As this concept is emerging within the AM community, an updated and thorough literature review will be conducted.
This work consists of multiple phases. We conducted a literature review, and identified a formulation of a liquid photopolymer resin that is capable of hosting scintillating dopants. For example, the work of Captain Baker and the USNA showed that commercially available resins from the 3D manufacturing vendor Formlabs (Somerville, MA) provide an acceptable base for mixing scintillating dopants. They found that scintillator material can be added to these commercial liquid photopolymer resins with little modification to the normal function of the 3D printer to produce an AM sensor that will effectively scintillate when irradiated with ionizing radiation. We have leveraged the recent advances of the USNA in our work. In addition, we have many of the Formlabs stereolithography (SLA) 3D printers used by the USNA team available for use at the NNSS.
Building upon the early work by the USNA, the next phase attempts to optimize the mix ratio of the resin and scintillating dopants. At this step, our team includes design review input from radiation physicists and nuclear engineers to specify the desired detection performance. This phase consists of multiple tests of different scintillators and includes performance comparisons to commercial off-the-shelf products from another collaborator, Eljen Technology. Eljen Technology is interested in using 3D printing technology for scintillator fabrication and has been a collaborator during this phase of our project. These tests were performed using the knowledge and expertise of the detector calibration teams here at the NNSS.
Results and Technical Accomplishments
During this project, our team has advanced our understanding of SLA resin printing. This includes the intricacies of the chemistry of the resins and how the mixing and doping of SLA resins affects the intricacies of the printing process. With this development, we were able to successfully mix scintillating dopants in the SLA resins. We tested two different mixtures, each suggested in collaboration with other researchers and industry, USNA and Eljen Technology, respectively. The USNA mixture contained anthracene and the Eljen mixture contained a combination of 2,5-diphenyloxazole (PPO) and 2,5-bis(5-tert-butyl-2-benzoxazolyl) thiophen (BBOT). We were able to verify a response due to incident gamma radiation in both of these samples. As compared to EJ-232, the response was about 3–4% of the output, but these preliminary mixtures show some promise. We have determined that the decreased response may be attributed to light transmission, whether it be from surface polish/finish or absorption in the bulk material, both of which are items to improve this next fiscal year.
Conclusions and Path Forward
This SDRD was able to produce AM samples that could detect gamma radiation. For the next phase of this project, we plan to improve performance and sensitivity of these AM samples. There are different concentrations and combinations of dopants that could increase this sensitivity, and close collaborations with our partners could help exploit those. We also plan to investigate other resins/printers that cure at different wavelengths or other printer technologies that can utilize different host materials. Also, we will start to integrate these AM samples with other hardware features and include modeling and simulation of ray tracing for integral light guides and the capability of using as a host for the design of pixelated/discriminating detectors.
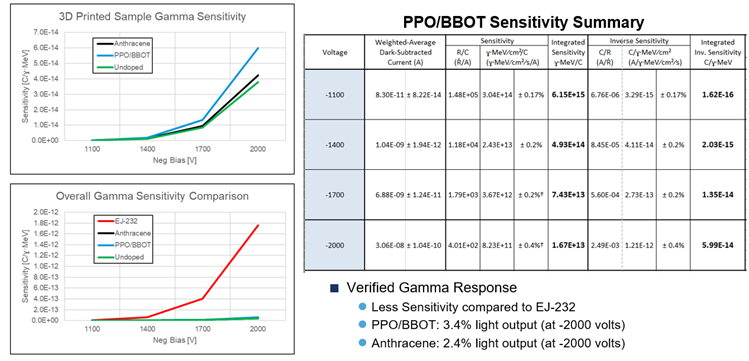