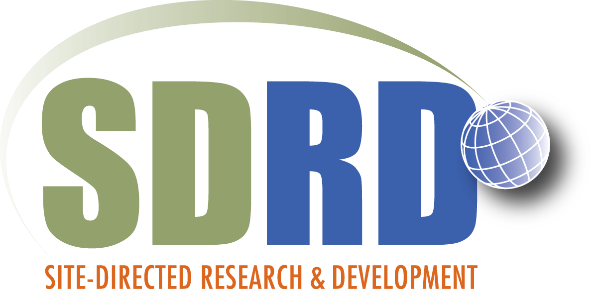
Health Assessment and Performance Monitoring of Large Machine Diagnostics
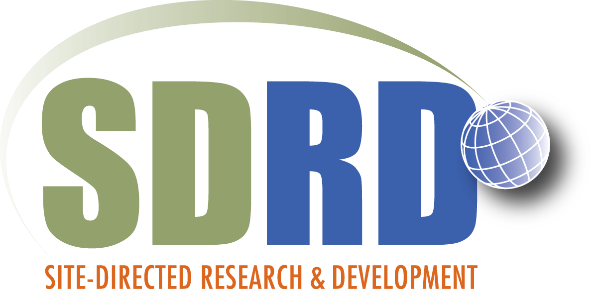
Project #: 22-119 | Year 1 of 2
Marylesa Howard,a Jesse Adams,a Margaret Lund,b Nolan Moore,a Daniel Mortenson,a Arnulfo Gonzalez,a Eric Jamesona
aNevada National Security Site (NNSS); bPacific Northwest National Laboratory
Executive Summary
Regularly maintained and operated diagnostic machines are the backbone of data collection within the National Nuclear Security Administration. In the event of a system failure during a dynamic experiment of the Cygnus x-ray system, too few, or no, x-rays are produced, resulting in an unacceptable failure to capture required data. Time and cost of preventative maintenance prohibit the prevention of all potential failures of large machine diagnostics, thus it is essential to monitor the health and performance of Cygnus to address system issues before a performance failure. The Cygnus team has collected voltage and current measurements at various points on the system for years, and these data contain predictive power to assess the health and performance of Cygnus. This project seeks to monitor machine performance prior to component failures by modeling the health of Cygnus through assessment of consecutive current and voltage measurements. We have also pursued a new diagnostic to specifically monitor capacitor health and performance.
Description
For every execution of a Cygnus axis, current and voltage measurements are collected throughout the pulse creation chain, clocking in at about 20 diagnostics per axis. We have identified three progressively complex questions to answer in order to determine our ability to assess the health and performance of Cygnus. First, given an execution of Cygnus and the available diagnostic measurements, can we categorize the shot as good or bad, or predict the dose? Second, can we determine declining performance of Cygnus, in some capacity, before a bad shot occurs? Third, given declining performance, can we determine where in the machine there is likely to be a component failure? Each of these questions builds upon successfully answering the previous question, and failure to answer a question results in an off-ramp for the project.
Initial modeling of figures of merit from a subset of the diagnostics, excluding the pin diode data, gave evidence that we can predict shot dose. We excluded the pin diode data as those are currently used by the Cygnus team for an indirect measurement of the x-ray dose, and we were evaluating if other diagnostics provided similar predictive power. The profile of the pin diode data qualitatively indicates the dose and performance as well.
To address the second question, we obtained a subseries of Cygnus shots prior to a component failure. Namely, we looked at shots numbered 4729–4761, resulting in 29 shots per axis. Prior to this subseries, axis C1 replaced a failed capacitor, so we assume C1 behavior during this subseries to be of nominal performance, with no failures occurring shortly after the subseries completes, either. However, axis C2 had a capacitor failure directly after shot 4761.
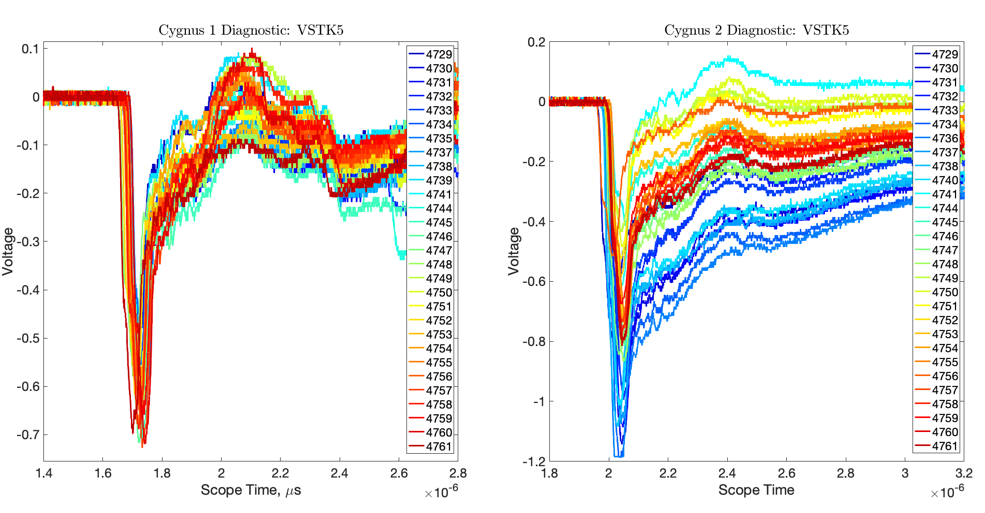
The figure above plots the Voltage Stalk 5 traces for this subseries, with the C1 axis diagnostic on the left and C2 axis diagnostic on the right. The profile behavior in C1 shows no temporal pattern, but the profile behavior for the diagnostic on C2 indicates a decreasing profile with time as we approach the capacitor failure. Modeling this behavior and moving on to question three are objectives for the second year of this project.
Furthermore, and specifically regarding capacitor failures, once a failure has occurred, simply identifying the failed capacitor for replacement can be a lengthy process, spanning multiple days, which negatively impacts schedule, increases cost of the experiment, and affects morale of the teams. To reduce this impact and assist in troubleshooting, we completed a proof-of-concept experiment in which we attached acoustic sensors outside a Marx tank and recorded the resulting sound waves from a modified hammer tapping at various locations on the machine, which allowed us to triangulate the originating location of the sound wave. In working with the company MISTRAS Group, we have commissioned an acoustic system, tailored for the Marx tanks at Cygnus, which will be a permanent installation for assessing performance of capacitors. While we expect this to help us pinpoint the location of failed capacitors, we expect that it may also contribute to pre-failure assessment of Cygnus when combined with the other voltage and current diagnostics being assessed in this project.
Conclusion
We have collected and curated the suite of diagnostic data for Cygnus, with initial models demonstrating our ability to predict dose and qualify performance of a Cygnus shot. This, in and of itself, is not revolutionary, but has allowed us to progress to more complicated questions about the predictive power of the data set. We have demonstrated a temporal behavior within some of the diagnostics that appears to correlate with future component failure. The second year of this project will seek to model this behavior and provide predictions to the Cygnus team as to locations of future failures within the machine. After a successful proof-of-concept, we have commissioned an acoustic system, designed specifically for the Cygnus Marx tanks, to monitor the health and performance of the capacitor banks.
Mission Benefit
The NNSS’ Cygnus x-ray system is a staple of the subcritical experiment program, providing high quality radiographs for National Weapons Laboratories. Component failures can result in catastrophic downtime for the diagnostic, affecting schedules, cost, and performance. For example, the age of the Cygnus x‐ray machine at U1a requires additional upkeep and maintenance, and a change in behavior (e.g., arcing in the water line) or failure of components (e.g., capacitors) can result in a few days, even weeks, of lost data collection due to troubleshooting and repairs. Building models to monitor the performance of a large machine using various measurements, like electrical current and voltage at multiple points on the path of the machine, may provide the ability to assess health, observe declining performance, and predict failures. Additional possibilities include assessments of symmetry for the diode itself, which contributes to the shot-to‐shot variance. A successful model serves as proof‐of‐concept and has potential to be extended to other large machines.
Publications, Technology Abstracts, Presentations/Posters
Howard, M. 2022. “Monitoring Health of Large Machines using Machine Learning.” Virtual Presentation. Rochester Institute of Technology’s Mathematical Modeling Seminar Series. March 2022.
Howard, M. 2022. “Monitoring Health of Large Machines using Machine Learning.” Virtual Presentation. University of Arizona’s Mathematics Graduate Student Seminar. March 2022.
Howard, M. 2022. “Health Assessment and Performance Monitoring of Large Machine Diagnostics.” Presentation. Los Alamos National Laboratory’s Statistical Seminar Series. July 2022. Los Alamos, NM.
This work was done by Mission Support and Test Services, LLC, under Contract No. DE-NA0003624 with the U.S. Department of Energy. DOE/NV/03624–1600.
Return to Accelerator Beam Science and Target Interactions
Go to SDRD Annual Report Index
Return to SDRD Homepage