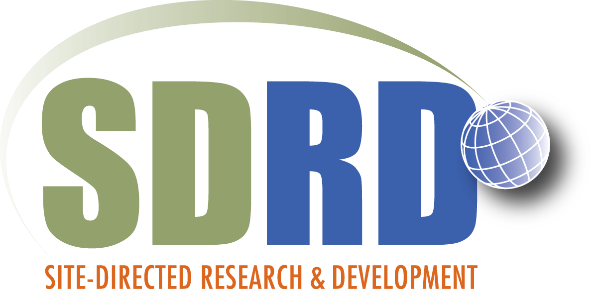
Solid-State Spectrographic Camera for HED and Pyrometry Applications
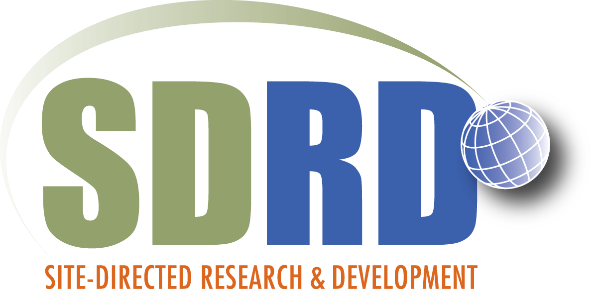
Project # 23-064 | Year 2 of 3
Amy Lewisa, Liam Clausb, Matthew Daytonb, Mike Jonesa, Kevin O’Flaritya, Ivan Pegrama, Marcos Sanchesb
aLos Alamos Operations (LAO), bAdvanced hCMOS Systems
This work was done by Mission Support and Test Services, LLC, under Contract No. DE-NA0003624 with the U.S. Department of Energy, the NNSA Office of Defense Programs, and supported by the Site-Directed Research and Development Program. DOE/NV/03624–1890.
Abstract
High-speed, nanosecond-scale, time-resolved radiance and pyrometry type measurements are essential to characterize advanced high energy density (HED) material tests at Z and the National Ignition Facility (NIF). Traditional streak cameras suffer from poor detector efficiencies, variation in temporal resolution from shot to shot and limited spectral range and overall sensitivity. A solid-state solution will provide a reliable, cost-effective option with improved performance. The proposed solid- state spectrographic camera will incorporate a complementary metal oxide semiconductor (CMOS) sensor with a novel shutter distribution architecture to create an imager with ~100-ps resolution. A prototype design will be submitted to the Sandia National Laboratories (SNL) Microsystems Engineering, Science and Applications (MESA) foundry as a ride-along to reduce cost and realize a camera in three years.
Background
This high-speed solid-state streak camera concept utilizes a standard two- dimensional focal plane array (FPA) architecture with a global electronic shutter. Standard FPAs collect spatial information in both the X and Y dimensions using an M rows x N columns array of pixels. The streak concept substitutes the spatial information in the X direction for temporal data, thus realizing an FPA that captures N, one-dimensional array images (of M rows of pixels). In this concept (Figure 1), an externally triggered, high-speed global shutter is generated, replicated, and then distributed to every row in the pixel array simultaneously starting at the leftmost column of the array (column0). Every column of the pixel array contains a delay element that will delay each subsequent column by a programmed delay time. Therefore, each column captures a one-dimensional image (of M rows) of spatial information while delaying the subsequent column shutter (image) by a delta-T on the order of 100-150 ps.
A time-varying input signal of photons is dispersed evenly across the image plane of the sensor using a cylindrical optic. A trigger synchronous to the experiment is issued to the FPA, and the image capture sequence begins. A rolling shutter propagates across the image plane capturing M linear array of images from the input signal starting at T0 and ending at TN. The two-dimensional pixelated read-out sensor array captures M rows of 1 × N images of the time-varying input signal are collected, illustrated in Figure 1. Consistent input impedance on every pixel is enabled by each pixel having a single signal connection to a corresponding photodiode via three-dimensional interconnect. The scalable architecture is limited to the size of the two-dimensional FPA.
Kathy Opachich, Hanna Shelton, and Minta Akin (Lawrence Livermore National Laboratory) have provided feedback for initial use case considerations.
.
Technical Approach
In the first year, the team developed a detailed camera architecture enabling a proof-of-concept design. The team modeled the readout integrated circuit (ROIC), detector, and system to predict performance under various input conditions and stimulus. The target design specifications for the new imager are presented in Figure 2. In the second year, the ROIC design was fully tested and submitted to the MESA foundry. Additionally, the design and layout of a corresponding photo- diode array was completed and submitted to the MESA foundry for fabrication. The camera test bench for the FPA will be designed before the end of Fiscal Year 2023. The electrical blocks of the test bench have been identified and design work underway at this time. All of the power supply integrated circuits (ICs), analog to digital converters (ADCs), and digital to analog converters (DACs), and the amplifiers have been identified. The schematic symbols for these parts have all been created in the test bed specific Altium library. The remaining work here is to create printed circuit board (PCB) footprints for the schematic symbols and to put the circuits together. The current plan for the sensor is to package it so it will connect to the testbed either via cabling or through board-to-board interconnect. This packaging will allow us to add cooling to the testbed, so we can get a sense of the noise performance of the sensor and the selected electronics together. The third-year effort will evaluate the solid-state streak imager designed in the first two years in a benchtop demonstration of the ROIC. The three- year proposal will yield a first-in-the-community solid-state streak camera with resolution suitable for dynamic experiments (in the 100-ps range) with a plan to achieve HED time scales in a second, programmatic iteration.
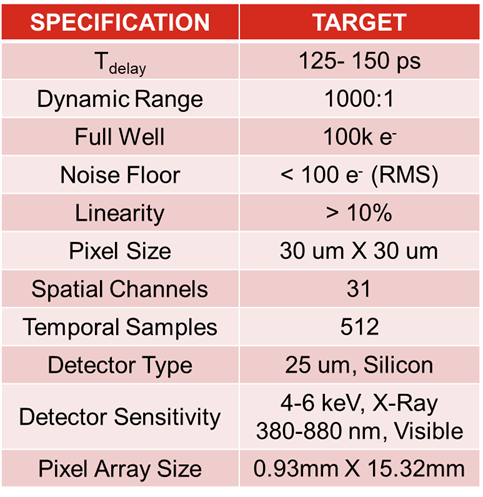
By using a two-dimensional FPA, different detector elements could be bonded to the ROIC to greatly expand the use cases of the camera.
Different detector types can be bonded to the Si ROIC using indium bump bonding or Direct Bond Interconnect (DBI). Detector options include silicon and GaAs targeting visible, x-ray, or energetic electrons. Fabrication and bonding costs can be optimized, as reticle size is shared with other Mission Support and Test Services ROICs/detectors. The integration time of the rolling shutter will be user programmable (0.1– 1000 ns). Typical streak camera time resolution is 30 to 100 ps per pixel and a nominal spatial range of 17 mm aperture. The proposed camera will target 100-ps range per pixel limited by the process (SNL CMOS7). The concept, if successful, could be ported to smaller technology nodes where propagation times are faster (20–50 ps). The proposed camera can have a 25–30 mm effective aperture limited by reticle size of the ROIC. Ride along with the Kraken reticle (~50–100 rows x 800 columns) limits the proof-of-concept device to 32 x 256 pixels. Detector fabrication, wafer testing, and hybridization costs will be largely diffused by the programmatic activity to produce the second version Kraken imager. The S4 design was integrated into the KV2 reticle, and the design has been taped out for fabrication as shown in Figure 2.
The CMOS7-based delay cell was designed and optimized for speed. Schematic-based design yielded 80-ps minimum delay, limited by the CMOS7 technology itself. Layout was performed and simulations conducted, including full parasitic extraction, and yielded 148-ps minimum delay. Typical layout parasitics reduce performance in CMOS7 by ~2x, so this falls within expectations.
Results and Technical Accomplishments
As shown in Figure 3, the design of the ROIC is complete and the team is awaiting fabrication at SNL MESA. The relatively inexpensive, solid- state streak camera will allow for new diagnostic opportunities in stockpile science and experiment collaboration with HED programs. A solid-state streak camera provides several advantages over traditional streak cameras, while the proven collaboration with SNL-MESA provides a good chance for success. This technology also leverages programmatic advances to manage cost and risk. Coupled with a solid-state silicon photodetector, the new imager will increase spectral range and detection efficiency (QE ~90% from 380 to 880 nm) to improve sensitivity and accuracy of radiance measurements.
Conclusions and Path Forward
A solid-state spectrographic camera capability would benefit many programmatic mission priorities in the following areas: HE-driven ejecta temperature measurements for melt equation of state (EOS) of ejecta or bulk materials in dynamic shock tests to inform physics models, HE and detonator performance tests, EOS for Insensitive High Explosives tests or high-temperature pyrometry on gas gun tests. Dynamic high-temperature measurements currently with traditional streak camera systems are also a critical diagnostic at Z, Omega, and NIF in the HED program.
Streak cameras have been workhorses in the weapons program for underground testing and subcritical experiments, as well as for university research. Very few flexible solid-state solutions exist for the wide variety of streak camera experiments. If successful, this camera design will create a significant opportunity for the Nevada National Security Sites to provide a state-of-the-art diagnostic system tailored to HED experiments.
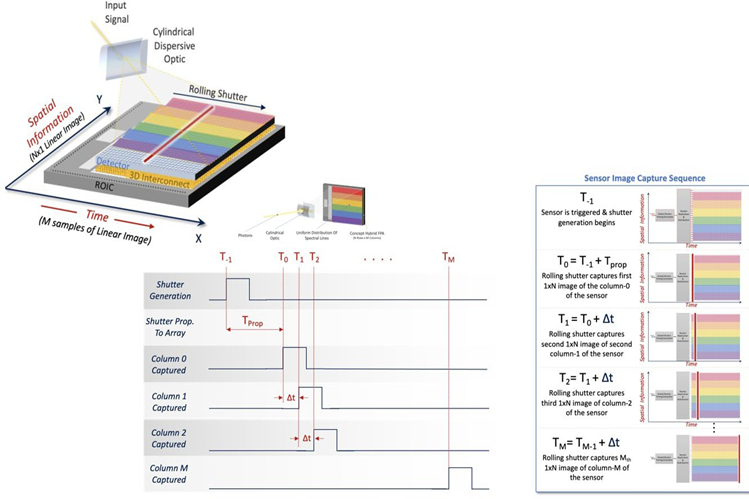
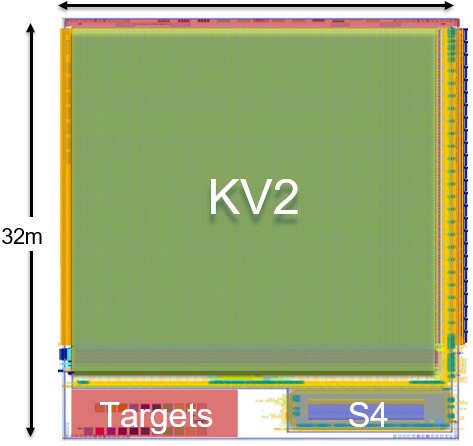
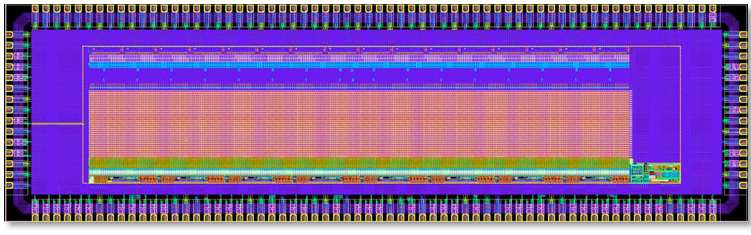