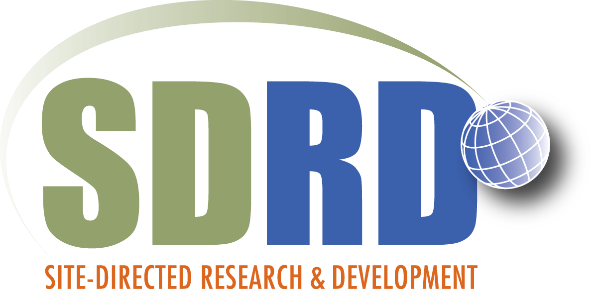
Thermal Transport Detection of Phase Boundaries at Elevated Pressures
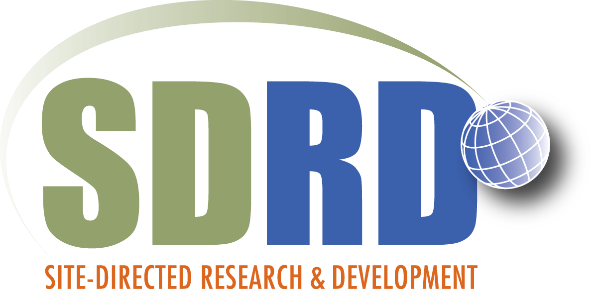
Project # 23-022 | Year 1 of 2
Rusty Trainhama, Brandon La Lonea, Matt Staskaa, Ruben Valenciaa, Paulius Grivicaksb, Allison Kuelz-Ackermanb, Thomas Hartsfieldb
aSpecial Technologies Lab (STL), bNational Lab: LLNL
This work was done by Mission Support and Test Services, LLC, under Contract No. DE-NA0003624 with the U.S. Department of Energy, the NNSA Office of Defense Programs, and supported by the Site-Directed Research and Development Program. DOE/NV/03624–1921.
Abstract
We are developing a new experimental technique to double-shock heat a compressible metal and use this hot layer to heat a thin metal coating on a lithium fluoride (LiF) window across a phase boundary. A similar technique was designed in a prior project (STL-031-21), and re-solidification of cerium was observed at the melt boundary—results1 were published in Physical Review B. This new technique offers the potential to explore high temperature melt boundaries in materials typically inaccessible on a powder gun.
Background
High temperature and pressure phase boundary determination typically is performed utilizing diamond anvil cells and x-ray diffraction. These experiments take place over long timescales of seconds to minutes. Dynamic determination of phase boundaries is difficult, and historically has utilized changes in wave speed at boundaries that create small features in velocimetry. We are using a method familiar to most from high school science. As you cross a phase boundary by heating a material (melting ice, for example), the rate of change in temperature ‘plateaus’ at the melt temperature.
Technical Approach
We shock, release, and re-shock a compressible material such as cerium or tin and have that layer of hot metal cross a gap and hold a thin (micron scale) film of metal under investigation against a transparent anvil at constant pressure, while thermal diffusion heats the film across phase boundaries. Temperature is measured using a technique we developed under the Site-Directed Research and Development program called Flashlamp Integrating Sphere Reflectance and Radiance (FISR&R). FISR&R uses a flash lamp to fill an integrating sphere, illuminate a shocked sample under a 6 mm LiF anvil window, and measure the dynamic reflectance of the sample. At the same time, we monitor radiance from the hot metal off to the side, in an area masked off from the flash-lamp illuminator. By combining dynamic radiance at 4–6 discreet wavelength bands along with reflectance in these bands, we can determine the dynamic temperature history of the shocked metal2.
Results and Technical Accomplishments
We performed four powder gun experiments evaluating the feasibility of this approach. The heating metal and metal under observation pairs for these were: cerium and aluminum, cerium and iron, tin and iron, and tin and LiF (direct impact). Each experiment reached temperatures far in excess of those predicted in hydrodynamic thermal diffusion models that were developed. This is likely due to instability growth from finely machined metal causing roughening of the shocked metal to develop as it crosses a 200-micron gap. This rough, hot metal then impacts the metal under investigation, causing localized penetration of the layer, and a heterogeneous temperature distribution to be viewed by our FISR&R system. This heterogeneity resulted in inconclusive temperatures; the multiple wavelength bands were not in agreement when temperatures for each were determined. The penetration also allows the hot metal to be viewed directly, perhaps explaining the unusually high radiance signals we measured. The figure below illustrates a CTH (Sandia National Laboratory’s 3-dimensional hydrodynamic code) model that shows the growth and penetration of cerium instabilities through an iron coating (our second experiment). The fourth experiment we performed was designed to observe the roughening of tin directly. Photonic Doppler Velocimetry (PDV) failed on this experiment. The tin likely became so rough that it scattered the laser light and returned no signal to our 2-fiber PDV probe. We have observed and published a paper on such behavior in the past3.
Conclusions and Path Forward
We have several approaches to mitigating the instability growth issues we faced in this first experimental series. First, reducing the gap will not allow such large features to develop prior to impact and second-shock heating of the hot layer. Next, we could ‘ring up’ launch tin across the gap. We may also shift our approach from shock, release, and re-shocking a metal to using a single shock on a two-stage gun with collaborators at Sandia National Laboratories. Despite these difficulties, our results are of interest to the shock-physics community that has been performing temperature measurements of thin film sample, and Fiscal Year 2024 experiments will provide additional insight into these phenomena.
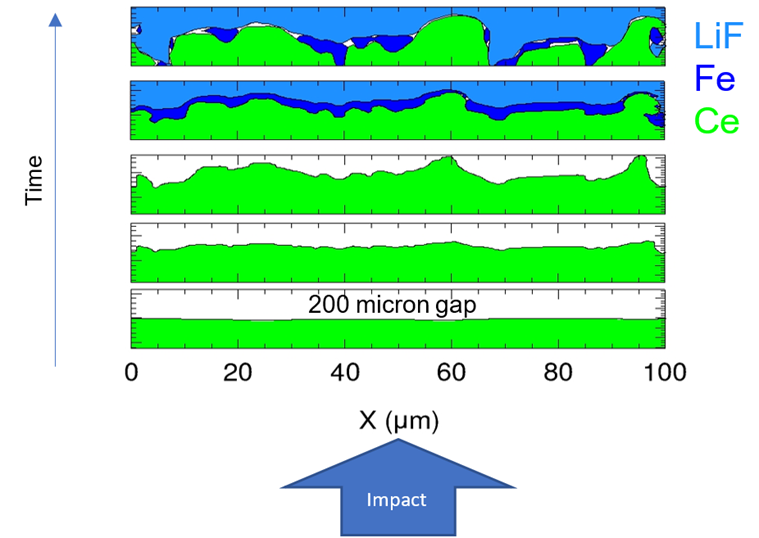
Publications
- Title: Temperature, enthalpy, and kinetics of cerium resolidification under dynamic compression
Journal / Conference: Phys. Rev. B 108, L140101
Year: 2023
Author(s): T. M. Hartsfield, B. M. La Lone, G. D. Stevens, M. T. Beason, J. K. Baldwin, and W. D. Turley - Title: High-pressure melt curve of shock-compressed tin measured using pyrometry and reflectance techniques
Journal / Conference: J. Appl. Phys. 126, 225103
Year: 2019
Author(s): B. M. La Lone, P. D. Asimow O. V. Fat’yanov, R. S. Hixson, G. D. Stevens, W. D. Turley, and L. R. Veeser - Title: Free-surface optical scattering as an indicator of the shock-induced solid-liquid phase transition in tin
Journal / Conference: J. Appl. Phys. 104, 013525
Year: 2008
Author(s): G. D. Stevens; S. S. Lutz; B. R. Marshall; W. D. Turley; L. R. Veeser; M. R. Furlanetto; R. S. Hixson; D. B. Holtkamp; B. J. Jensen; P. A. Rigg; M. D. Wilke