Training prepares students to fight accidental spills involving toxic materials.
With his hand covered in a bright green glove, and in full, head-to-toe protective gear, Nevada National Security Site (NNSS) Field Technician Shane Hodge reached into the top of the tank containing fuming sulfuric acid and turned the valve to the right.
It was the first in a series of steps that would transport the highly hazardous chemical down a pipe and into a controlled spill pan, giving students the opportunity to learn how to properly fight and clean up the material in the event of an accidental release.
“We supply the area for the students to work, create the ideal conditions for the training to take place, and they fight it,” said Kylief Tucker, Facility Manager for the Nonproliferation Test and Evaluation Complex (NPTEC) at the NNSS. “It’s the only place in the world where this kind of work can take place.”
The students came to the NNSS in June as part of a two-week, intensive training course for Veolia, which produces large amounts of highly toxic chemicals including oleum, chlorosulfuric acid and sulfur trioxide. These products are shipped via rail, truck, ships, and portable tank to customers both inside and outside of the United States. Small amounts of these chemicals are used in surfactants, which can be found in everyday essential products like shampoos and soaps, and in countless other consumer products that companies make across the country.
Due to the nature of the materials, spills in transit or at production facilities possess a high potential to produce a massive vapor cloud. Such spills could endanger employees who work with the chemicals, and could pose a risk to the broader public. The topography, wind predictability and location of NPTEC offers partners like Veolia a secure, controlled, and realistic environment for training students in how to mitigate those risks. All projects are conducted within environmental and safety regulations.
“We’ve shown over the years that the training at the NNSS is highly effective in reducing the severity of unintended releases,” said Brad Van Scoik, Operations Chief for Veolia. He said the company has used the services at NPTEC every two to three years since 1992.
The field training provides responders with hands-on practice so that when they’re called upon to respond in real-time to a spill, they have practical experience to back them up. Veolia, which specializes in environmental solutions, offers the training to its own employees, customers who use the products, and transportation and hazmat crews as part of its product stewardship mission to prevent spills and to develop safe spill remediation procedures.
From the control room, a couple hundred feet from the exercise area, NNSS Engineer Ryan Jensen and NNSS Training Specialist Larry Platte kept a diligently close watch on the computer screens in front of them. Data from weather stations across NPTEC capture the wind speed and direction, and populate the digital compass.
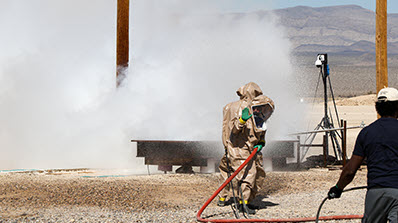
“It’s green,” said Platte. “We’re in the window.”
Winds must come from the southwest and be sustained for 30 minutes at 2 meters per second or higher in order for the exercise to be a go. That ensures the safety of all students and NNSS personnel on site.
“The system is armed, valves are open, the tank is pressurized,” Jensen relayed to the NNSS team.
He clicked a button on the process control system – and then a second pop-up to confirm his decision – to open the final valve, which released the fuming sulfuric acid. It was the first practice spill of the day.
Four students formed the strike team. Clothed in chemical-resistant, fully encapsulated suits fashioned with a breathing apparatus, members of the team approached as the chemical hit the spill pan, and a massive, white cloud ballooned into the air.
Using fire hoses in a sweeping, back-and-forth motion, the team first hit the acid with water in an effort to dilute the chemical, which can reach over 500 degrees Fahrenheit.
Next, they doused the chemical with Spill X – a powder-like substance that neutralizes and solidifies the acid.
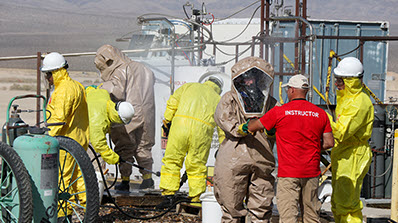
It took only a few minutes for the team to neutralize the material to a pH level of 8 – the magic number is anywhere between a pH of 2 and 12 – and then shoveled the now-safe material into waste barrels.
“Every time we come out here we’re learning new techniques and trying new things to make sure we stay on the cutting edge of mitigation measures, and to make sure they will work out in the field,” said Van Scoik, who served as the incident commander for the exercise.
For example, this year students practiced with a cleaner, fluorine-free firefighting foam to see if it would knock down the plume of chemicals as quickly as its fluorine counterpart. They also practiced with a hand-held foam machine, which they had not yet used on a spill.
In total, the students practiced mitigating 21 spills over the two weeks.
“We want to protect our communities and our environment and this training helps us to do that,” said Veolia Project Director Alec Myers.