Navarro, contractor to the U.S. Department of Energy (DOE) Environmental Management (EM) Nevada Program, is celebrating 12 years without a lost workday.* This continuing safety record was accomplished while leading the EM characterization and remediation work scope, which addresses environmental impacts of contamination resulting from historic nuclear testing at the Nevada National Security Site (NNSS) and Nevada Test and Training Range (NTTR).
EM characterization and remediation involves workplace hazards such as heavy machinery, radiological contamination, unexploded ordinances, work outdoors in excessive heat and extreme weather conditions, and the slips, trips and falls that are present in every workplace. Twelve years without serious incident is a remarkable accomplishment.
In carrying out EM Nevada Program missions, Navarro employees who work onsite at the NNSS and NTTR are tasked with developing groundwater characterization wells, surveying Soils and Industrial Sites for contamination, excavating land, demolishing structures, and disposition of waste. Like all DOE contractors, Navarro adheres to the Integrated Safety Management Policy, which ensures that safety is integrated into management and work practices at all levels and stages of planning and execution.
Navarro workers attribute their safety record to a number of factors, including meticulous planning, detailed coordination with other contractors and DOE federal staff, deliberate pace of work, prioritization of safety and an experienced workforce.
According to Navarro’s Health and Safety Manager Gregg Mickelson, up-front planning is key. “Hazard analysis always includes all personnel involved, from management, to the Health and Safety department, to the people who will be out there working in the field. Everyone has an awareness of the potential hazards,” Mickelson said. Without exception, every day in the field starts off with both a daily operations call and a Tailgate Safety Briefing, during which workers review procedures, acknowledge potential hazards and address safety measures.
Juvencio “JC” Castro explains that working at a deliberate pace is an effective preventive measure in avoiding accidents. “Due to the nature of our jobs, we have to move slowly to get the work done correctly,” said Castro, a radiological control technician working on the Soils project. Groundwater Characterization Program Site Supervisor Steve Hopkins shares the same sentiment. “We are not out to set speed records,” Hopkins said. This deliberate pace of work is expected by management and adhered to by field workers and results in careful, safe completion of tasks.
One of the most important aspects of the safety culture at Navarro is prioritization of safety over production. Dan Henry, site supervisor for the Soils project, described a typical summer workday in the desert environment of Nevada, which regularly reaches temperatures over 100 degrees: “There isn’t pressure on how much work is performed; instead, on a hot day, the pressure is focused on taking enough breaks to stay safe and healthy.”
“Safety over schedule,” is the motto of the workers and managers, according to Dawn Peterson, Navarro’s Closure Support manager. Peterson is in charge of scheduling workers’ shifts in the field. “We also have extra workers on site so that no one is rushing under pressure to get a job done,” Peterson said.
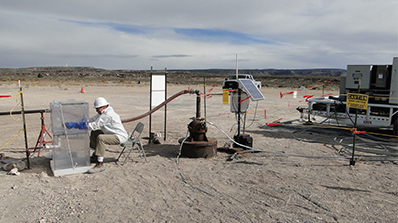
Another major component of Navarro’s safety culture is its experienced workforce. Many Navarro employees have been working in various roles within the EM Nevada Program for decades. The unique hazards specific to their worksites are well-known, and the experience gained over many years in the field allows accident prevention to become second nature. In addition to technical experience, long careers spent working on EM Nevada Program missions lead to strong relationships between employees who have worked side by side for years. These relationships enable workers to recognize each other’s strengths and weaknesses, look out for one another, and respect each other’s instructions, cautions and advice. Ultimately, a collaborative environment is built where every worker takes responsibility for their own safety as well as the safety of their coworkers.
Workplace safety is no less important to Navarro employees who spend all or most of the workday in the office. Dona Merritt, of Navarro’s Strategic Communications group, distributes reports of reported workplace safety incidents from around the DOE complex to team members. “Sharing and reviewing these occurrences is part of a learning process to improve our awareness of potential safety issues,” Merritt said.
The Strategic Communications group often travels to outreach and community events across southern Nevada to provide the public with information about EM Nevada Program activities. Safety procedures are always strictly followed, from safe driving practices, to proper techniques for loading and unloading the supplies needed for events. “Safety culture is promoted and embedded in every aspect of planning work, even in the office. Looking out for potential hazards has become routine. It’s so much a part of who we are as Navarro associates, that we take it home and make our home lives safer, too,” Merritt said.
These various components add up to a culture of safety in the workplace that permeates every job site, office, and cubicle. Dave Taylor, Navarro’s program manager, has championed this philosophy with regular Safety Leadership Training meetings and other programs that emphasize the importance of safety, as well as facilitate and encourage reporting potential hazards or safety concerns. “We had to develop a consistent philosophy that supports a culture of doing work safely, and then reinforce those values over and over. Once you get something in place that works, you can never let up,” said Taylor.
*A lost workday is an occupational injury or illness which results in an employee being unfit for work on any day after the incident.